Mussel Farming
At the heart of Tidal Marine’s approach is the individual drop “sock” method. This system employs “Droppers” that are strategically hung from submerged longlines, surface longlines, or rafts. Renowned for its low capital investment and straightforward design, this method has transformed how mussels are cultivated.
The Tidal Marine system is meticulously structured to enhance mussel growth and ensure high-quality harvests. It starts with meticulous seed collection, followed by de-clumping and grading to ascertain uniform seed sizes. By controlling densities during the socking process, we not only optimize growth but also ensure uniformity in the size of mussels at harvest. This precision allows for staggered harvesting, maintaining continuous production and quality.
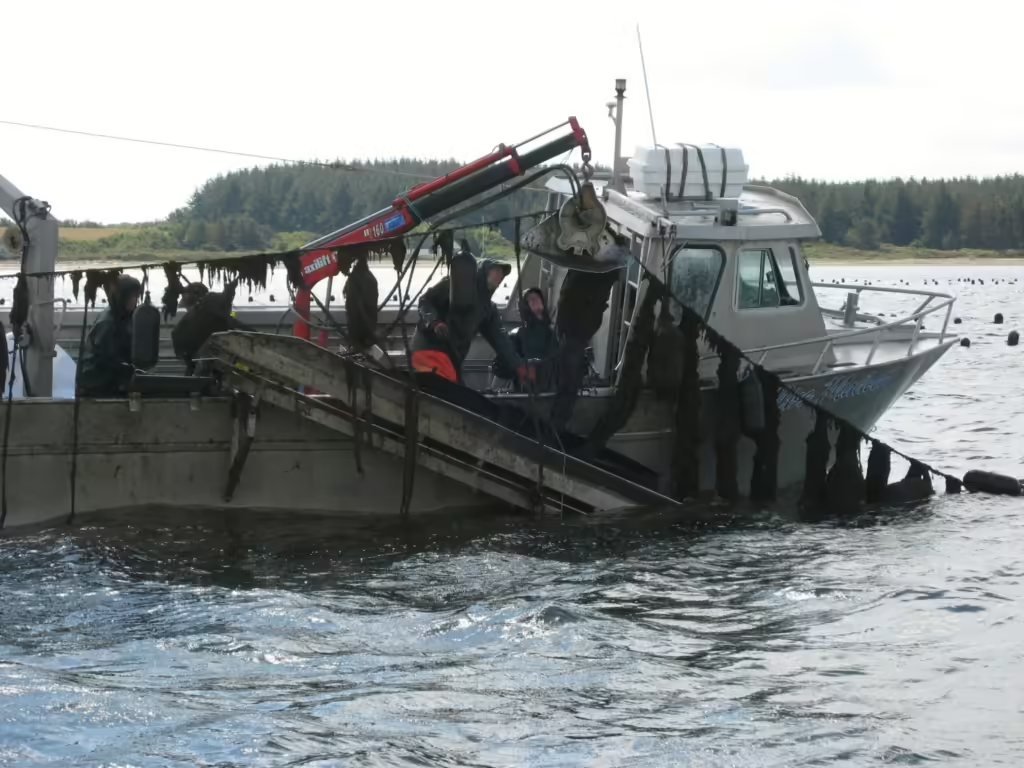
Small operation workboat harvesting Tidal Marine Mussel Socks.
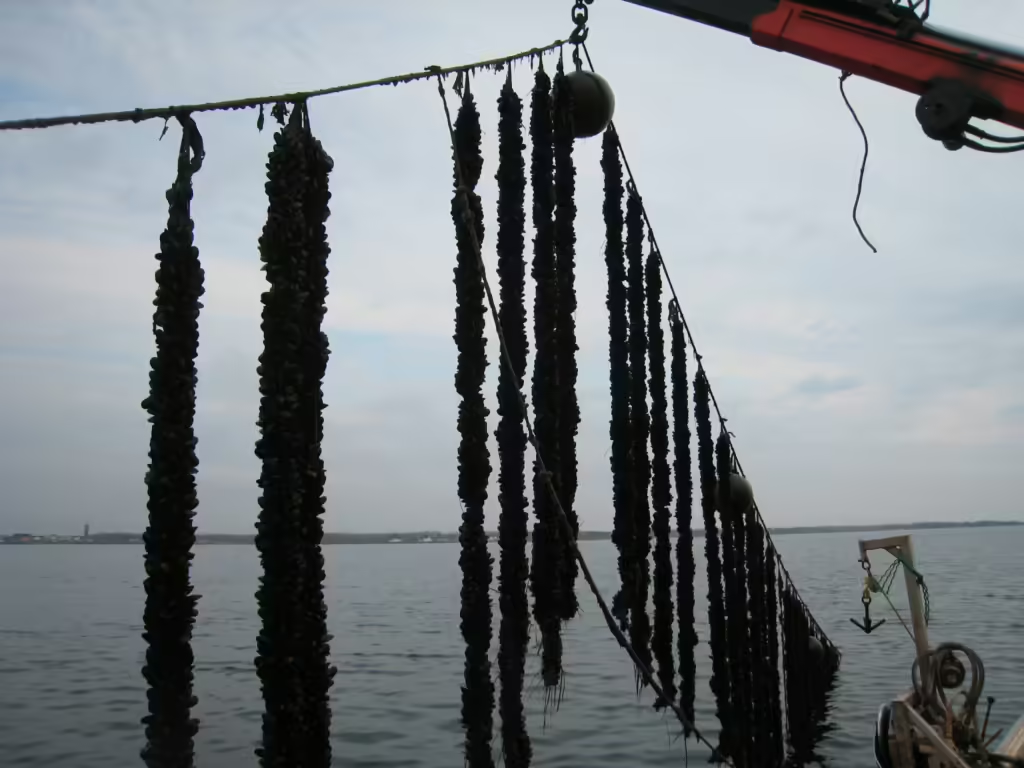
Lifting the submerged longline with Tidal Marine Mussel Socks.
Benefits of Our Socking System
Key advantages of our mussel farming system include improved seed retention from grow-out to harvest and significantly reduced losses due to size variability at the final grading stage. This efficiency ensures that investments in flotation and equipment are maximised, supporting only the growth of marketable mussels. Consequently, this reduces the number of mussels discarded or sold at a lower price due to non-uniform sizes.
Designed with the user in mind, our mussel socking process is straightforward. Controlling seed density during the “socking” phase is seamless, thanks to the uniform seed size achieved during grading. We offer various diameters of socking tubes to match different seed sizes, ensuring a consistent number of mussels per linear length of sock, which facilitates predictable growth and harvesting cycles.
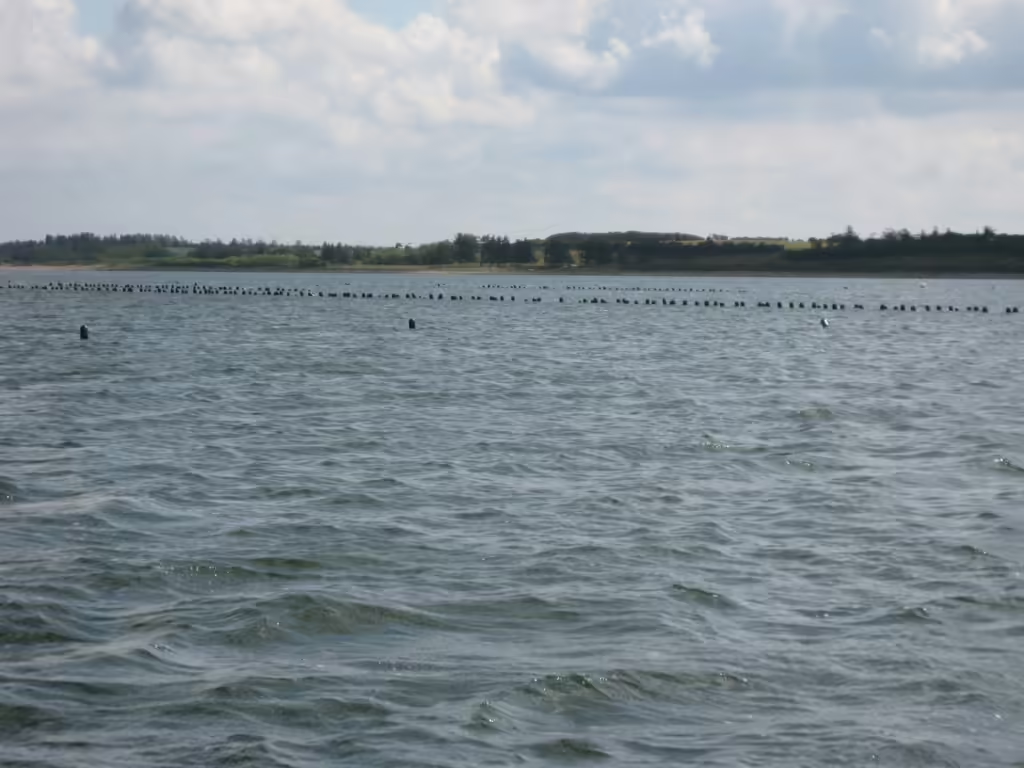
Grow out longlines are submerged. Only the surface seed lines are visible.
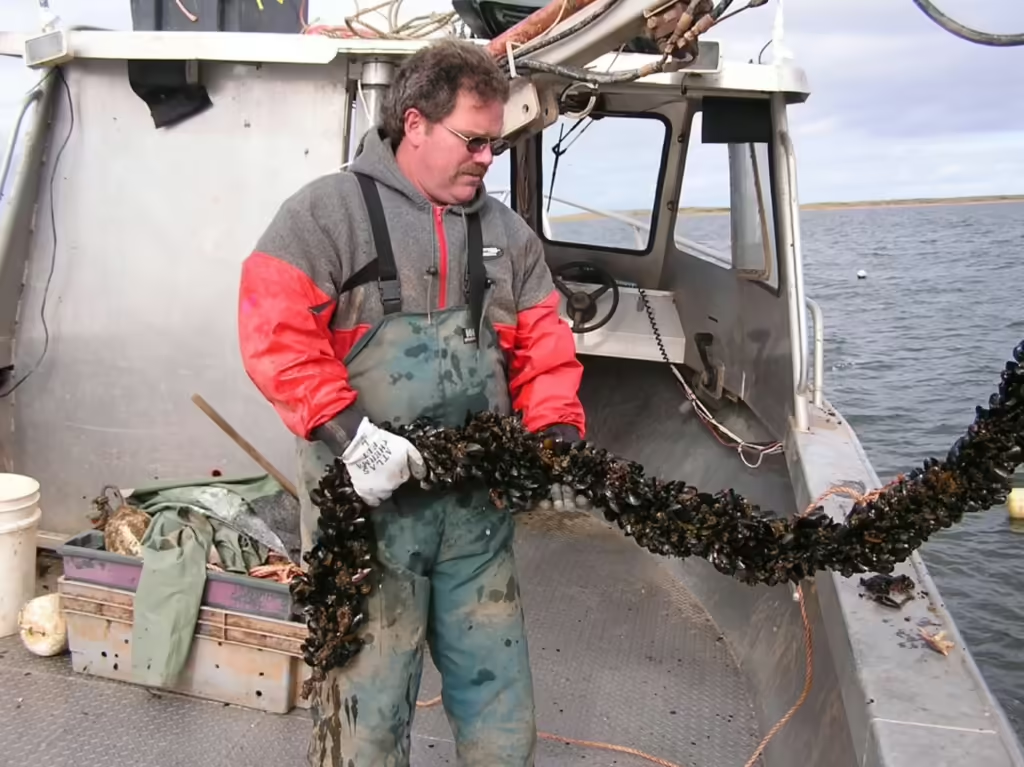
Inspecting Tidal Marine mussel socks during grow out phase.
A submerged longline system is commonly used to reduce the impact of storms and heavy seas, to allow mussel farming in areas that experience ice during the winter months, and to eliminate visual concerns from local landowners.
Submerged longlines offer a number of benefits:
- They utilise 100% of the flotation buoyancy, which reduces flotation costs.
- They eliminate excess buoyancy/stored energy associated with surface flotation longlines, which can cause product loss and equipment damage during storms.
- They can be set up to eliminate sagging between buoys, allowing their use in shallow waters.
Through these methods, submerged longline systems not only foster a more robust and resilient mussel farming operation but also integrate well into diverse marine environments, promoting sustainable practices that benefit both the ecosystem and the local communities.
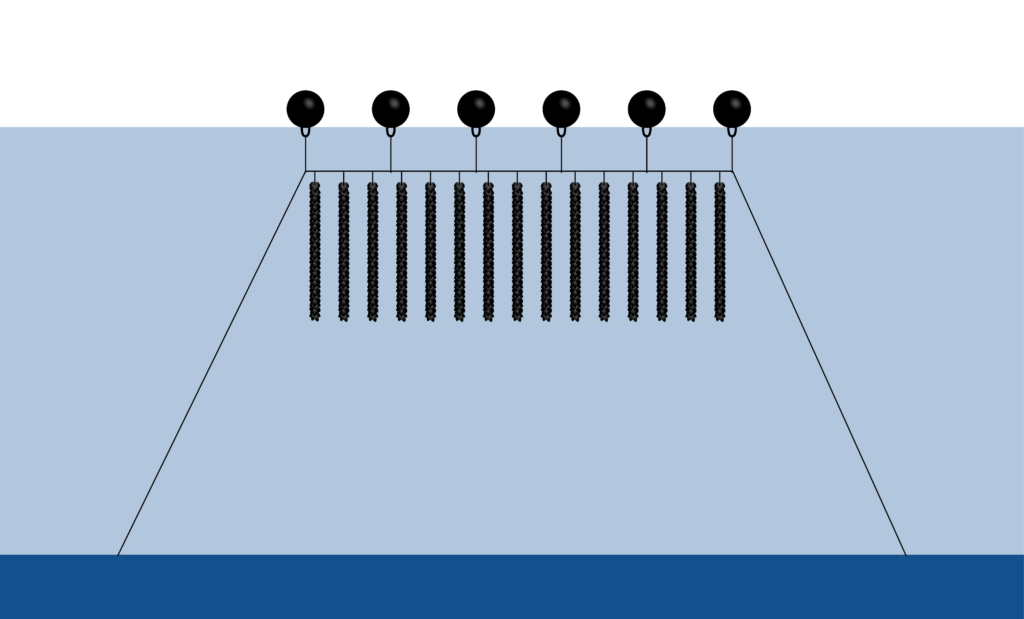
Illustration of Surface Longline (not to scale).

Illustration of Submerged Longline (not to scale).
Anchoring the Longline
The stability of a submerged longline starts with its anchorage. Depending on the type of seabed, different anchors are utilised to secure the longlines effectively:
- Helical Screw Anchors: Ideal for firm seabeds, these anchors screw into the substrate to provide a strong hold.
- Embedment High-Hold Dual Shank Anchors: These are used for softer seabeds and offer enhanced stability due to their dual shank design.
- Deadweight Anchors: Suitable for various bottom types, these anchors rely on their weight to maintain position.
Mooring and Tension Management
Connecting the anchor to the longline is the mooring scope line, which is crucial for maintaining the correct tension and alignment of the longline. The length of the scope line is determined by the water depth and the type of anchoring used. Scope line buoys are strategically placed to ensure the longline maintains proper tension and alignment.
Depth and Buoyancy Control
The depth at which the longline is submerged is carefully calculated based on environmental conditions and the specific requirements of the mussel farming operation:
- Pressurised Longline Buoys: These are installed at regular intervals along the longline. Their role is to provide positive buoyancy, supporting the weight of mussel socks and ensuring that the mussels remain at the optimal depth for growth.
- Deadweight Blocks: These are placed along the longline to finely tune its depth. The blocks are heavy enough to counteract the buoyancy and maintain the longline at the desired depth, allowing the mussels to thrive in their marine habitat.
These systems not only support the growth and health of the mussels but also ensure that the operations can withstand diverse marine conditions.
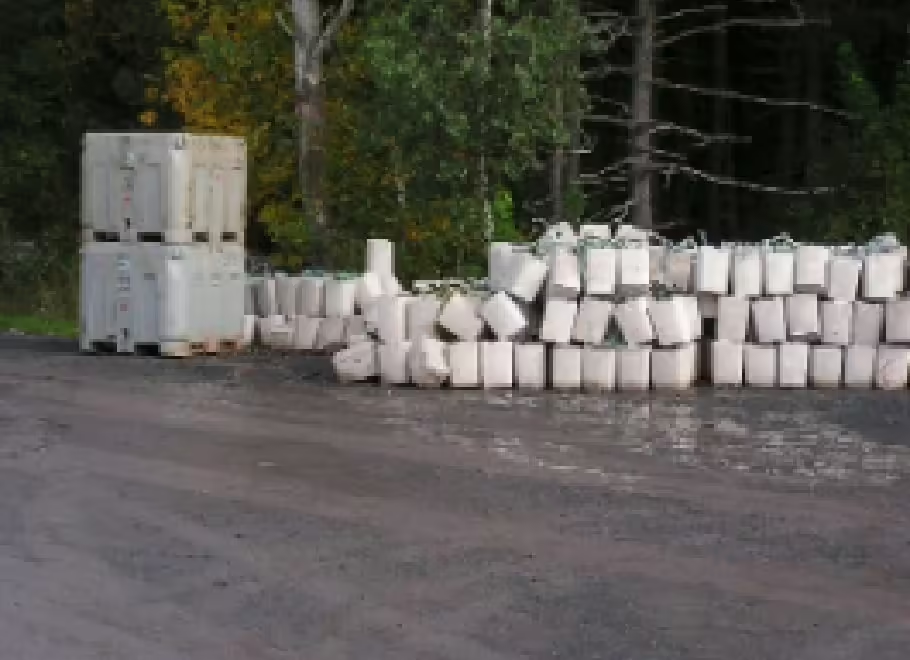
Deadweight Anchor Blocks.
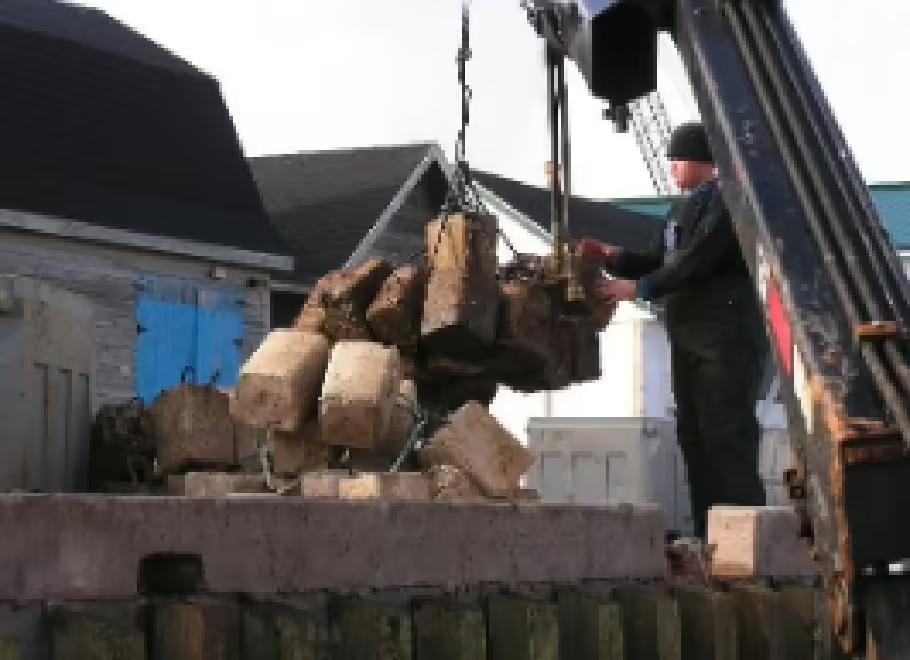
Transfer Deadweight Anchor Blocks to Vessel.
Navigating and Managing Buoyancy in Submerged Mussel Farms
Submerged mussel farms utilise a sophisticated system of pressurised buoys to ensure both the productivity of the mussel crops and the safety of operations above.
Safe Navigation Above the Farm
Pressurised buoys are strategically attached to the longline at depths that allow operational vessels to navigate safely above without interference. This careful placement ensures that the farm remains protected from potential disruptions caused by surface traffic, while also allowing easy access for farm management and maintenance.
Dynamic Buoyancy Adjustment
As mussel crops grow, their increasing weight can cause the longlines to sink lower than ideal for their growth or vessel safety. To counteract this:
- Adding Additional Buoys: Initially spaced buoys may become insufficient to support the added weight of maturing mussels. Additional buoys are inserted between the existing ones to enhance buoyancy and maintain the longline at an optimal depth.
- Monitoring with Depth Sounders: Operation vessels equipped with depth sounders regularly pass over the submerged lines. These instruments help determine the current depth of the longlines, signaling when it’s time to adjust buoyancy by adding more buoys.
- Visual Depth Indicators: For an immediate visual assessment, small diameter spar indicators may be attached at intervals along the longline. These indicators protrude above the water, allowing crew members to easily observe the longline’s depth and assess whether additional buoyancy adjustments are necessary.
The Process of “Buoying Up”
This ongoing adjustment process, known as “Buoying Up,” is crucial for maintaining the health of the mussel crop and the efficiency of the farm. By regularly assessing and adjusting the buoyancy, farmers can ensure that their mussels grow in an environment that promotes optimal health and productivity.
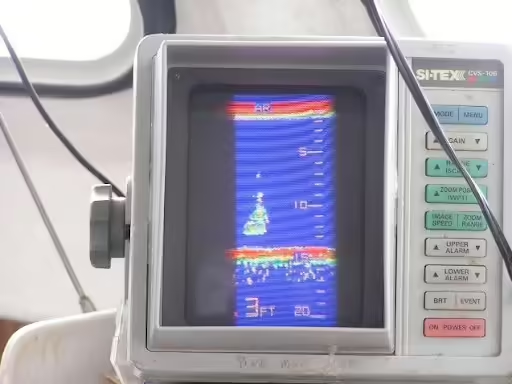
Transfer Depth Sounding to Determine the Depth of Longlines.
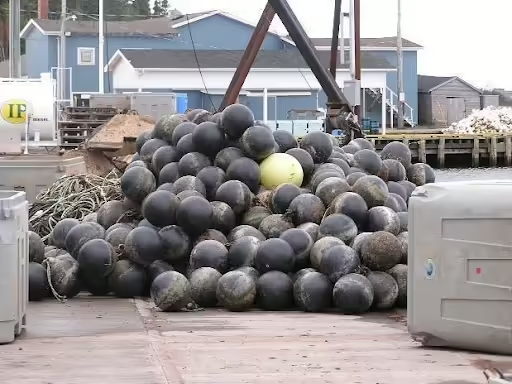
Pressurized GoDeep Buoys
The longline and mooring line provide sufficient scope, allowing the longline to be lifted to the surface at any point along its length. A grappling hook is lowered to secure the longline, which is then winched to the surface and placed in a Star Wheel Hauler. The vessel can then proceed along the longline, raising it to attach mussel socks and additional buoys.
Once installed, the longlines with their initial buoys and dead weights will remain functional for many years, requiring only occasional maintenance operations such as re-tensioning. Employing more expensive, high-tenacity, low-stretch ropes can minimise the need for frequent re-tensioning.
Our pressurised longline buoys have been in use for over thirty years, with many of the original buoys still operational. These buoys are manufactured using a proprietary polyethylene and master batch system and are available in two depth ratings:
- Surface to 10 m depth
- Surface to 20 m depth.
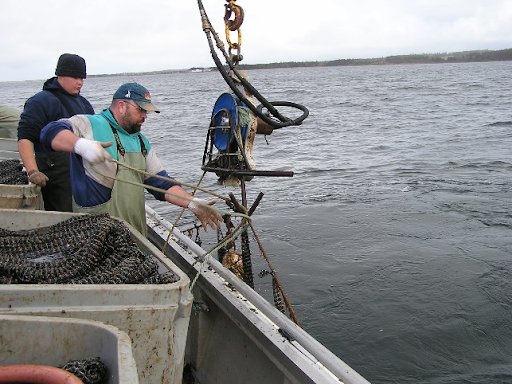
A grappling hook and winch are used to bring the longline to the surface.
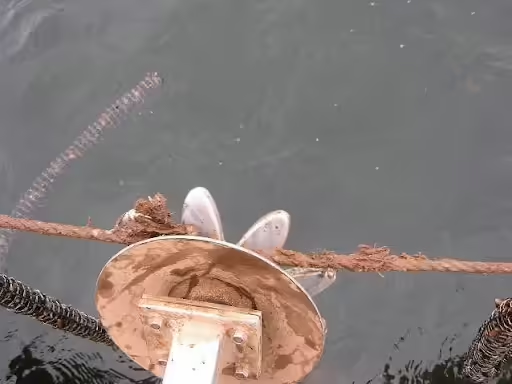
A star wheel raises the longline as the vessel advances.
Mussel farming is a dynamic industry tied closely to the rhythms of the tidal marine environment, where the practices of seed collection and grading play pivotal roles. These techniques not only enhance the efficiency of mussel farming but also contribute significantly to the sustainability of this aquaculture sector.
Optimising Seed Collection for Quality and Efficiency
The process of seed collection and subsequent grading offers numerous benefits, most notably producing a consistent size of mussels at harvest. This uniformity is crucial as it allows for varied harvesting timelines and reduces handling costs. By separating and grading mussels when they are smaller and lighter, farmers can manage their crops more effectively and efficiently.
Grading and Re-socking: Ensuring Consistent Yields
Another critical step in mussel farming is the re-socking and grading of mussels. This practice enables farmers to achieve consistent yields in terms of size and count per meter of mussel line, which significantly enhances the value of the crop at the market stage. Through careful grading at the processing level, farmers can ensure that only the best-quality mussels reach consumers, thereby maximising their market potential.
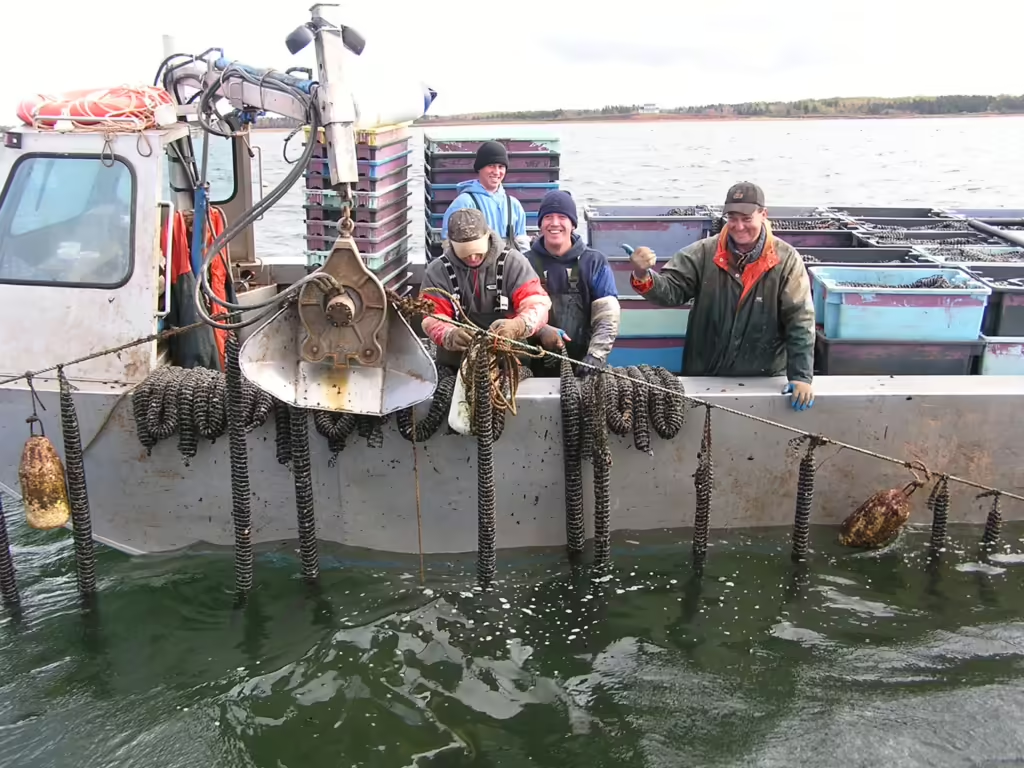
Mature seed line.
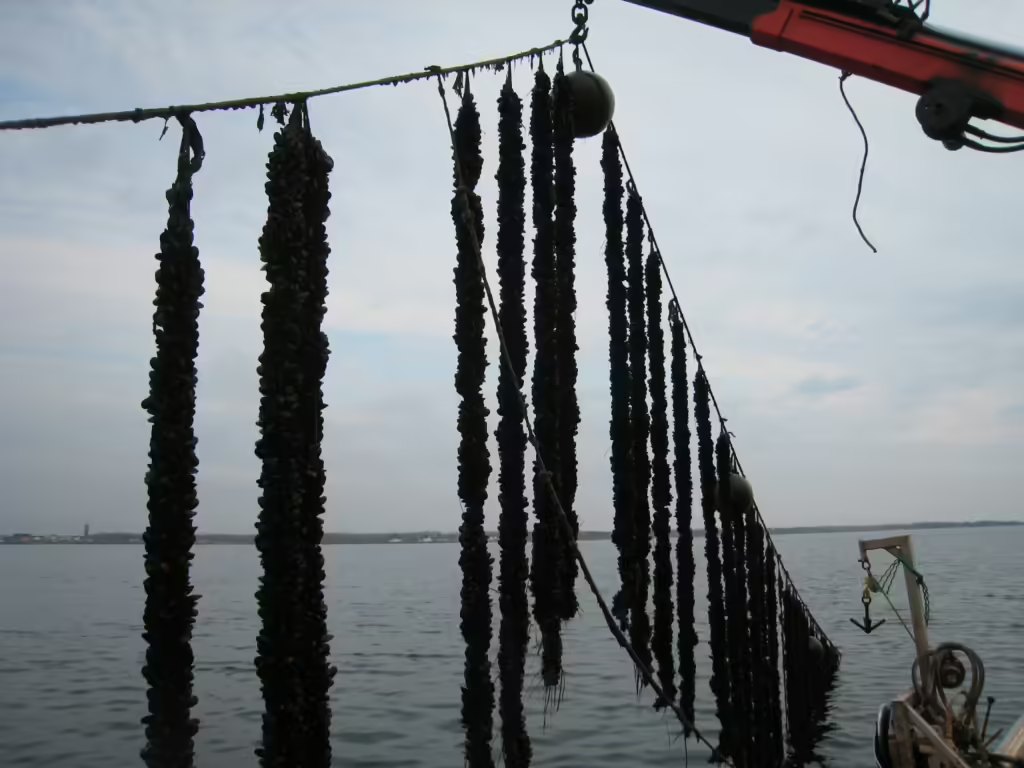
Inspection of surface collection seed line.
Exploring Materials for Ideal Seed Collector Substrates
Farmers continually experiment with various materials to find the most effective seed collector substrates. Popular choices include used and fuzzy ropes, which have proven successful in supporting mussel spat attachment and growth. These collectors are typically suspended from surface longlines, strategically deployed just before the expected spat settlement period.
The Role of Surface Longlines in Mussel Farming
Surface longlines, utilised with smaller buoy systems, are deployed for approximately four to six months. This duration allows ample time for the mussel spat to settle and mature enough before the subsequent phases of harvesting, de-clumping, and grading for socking in Grow-Out Mussel Socking Tubes.
Streamlining Operations and Handling
The process of stripping mussel seed from collectors onto handling bins aboard vessels marks the transition from sea to shore. This method is particularly prevalent in nearshore farming setups where operations can be streamlined using land-based facilities equipped with essential utilities like power and water.
Diverse Farming Operations
Mussel farming operations vary significantly in scale, ranging from small setups producing 200 metric tons to large operations handling up to 12,000 metric tons per year. The size of vessels also varies considerably, from 26 feet to 70 feet in length, which influences the methods and containers used for seed handling—from small 30-litre totes to large 1000-litre boxes equipped with lids for crane operations.
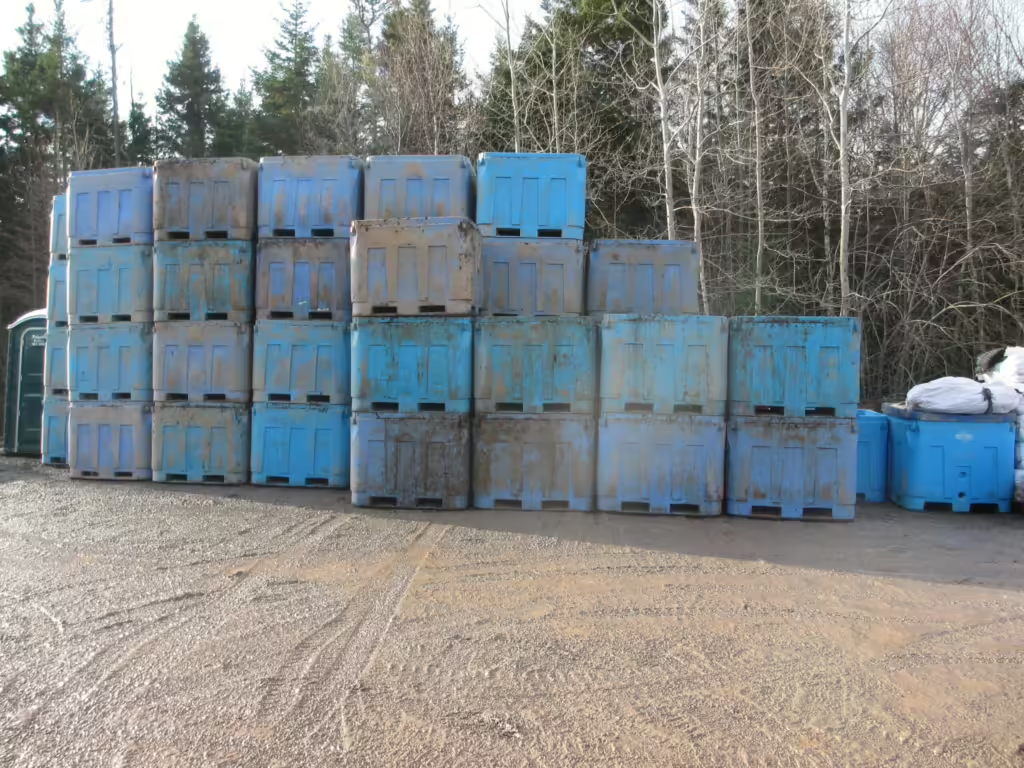
Large Operation Using 1000 L Handling Bins.
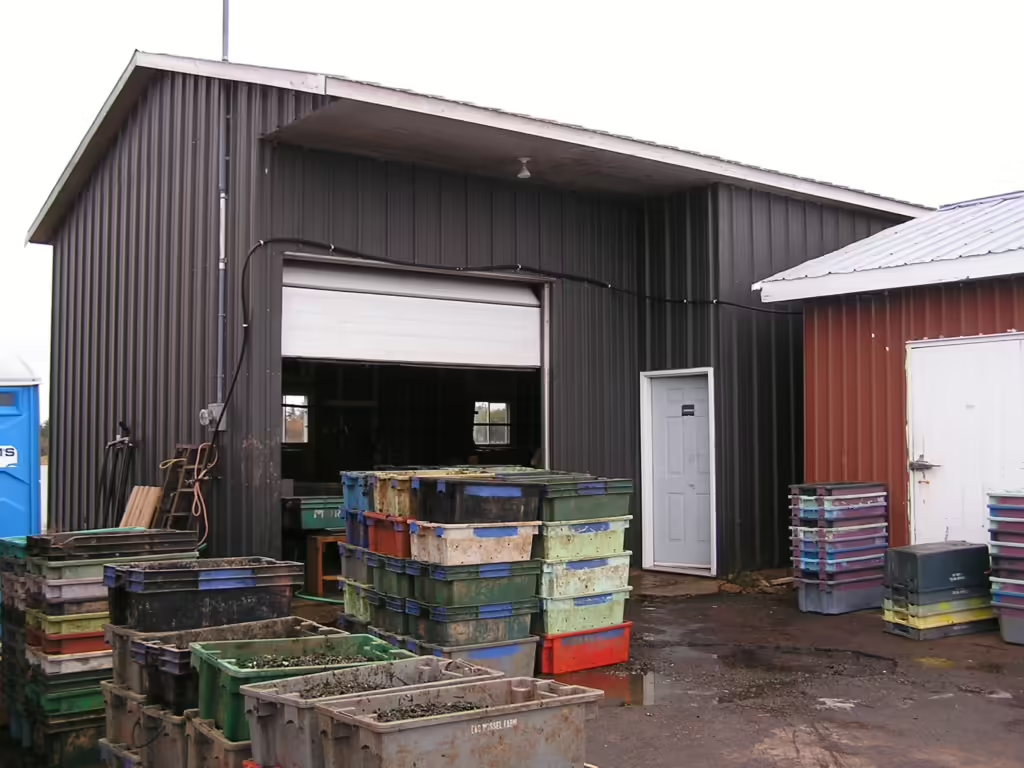
Small Operation Using 30 L Totes.
Mussel farming is a meticulous process that starts with an essential step known as seed grading. Let’s explore how this procedure helps in enhancing the productivity and uniformity of mussel harvests.
Step 1: Declumping the Seeds
The initial phase in seed grading involves the separation of mussel seeds. This process, known as declumping, is crucial as it prepares the seeds for subsequent sizing. The seeds are gently conveyed from the declumping machine to the grading equipment, ensuring minimal damage.
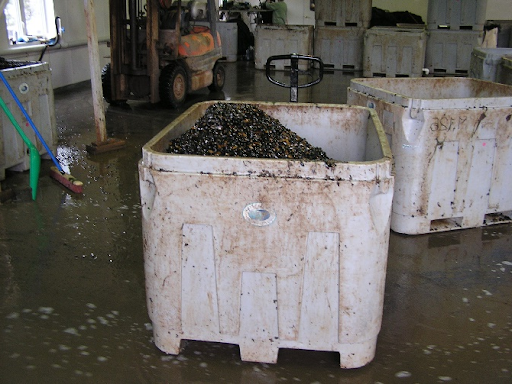
Seed stripped from collection lines to be declumped.
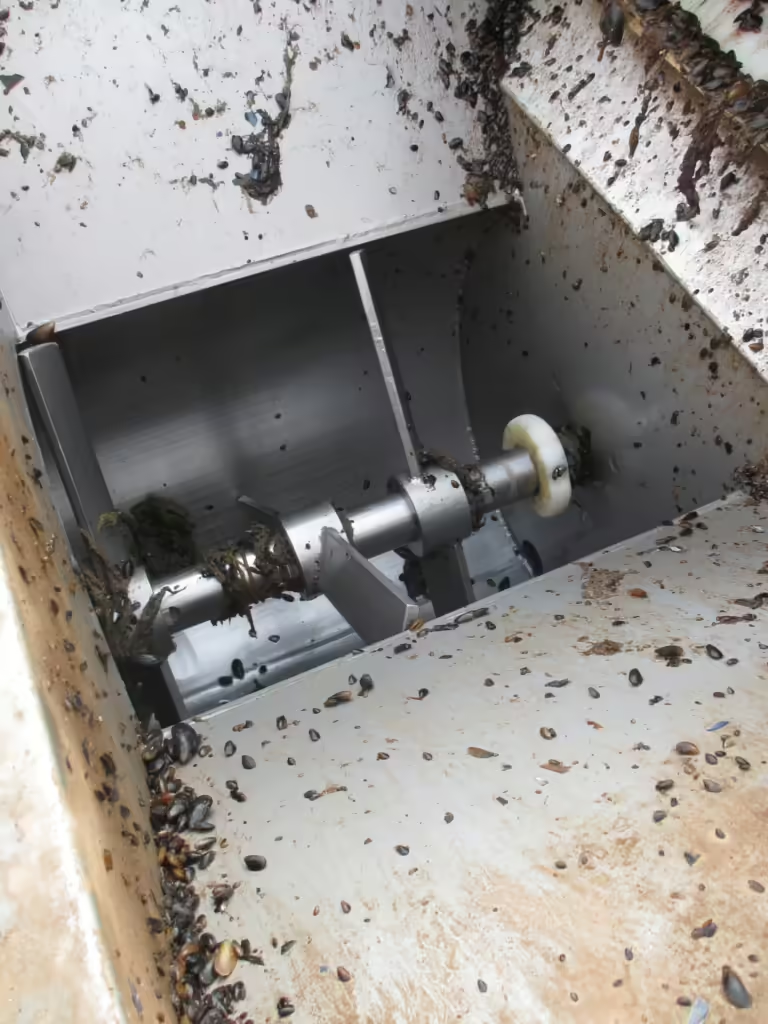
Rotating declumper bars.
Step 2: Grading the Seeds by Size
Following declumping, the seeds are sorted by size using specialised equipment. This apparatus typically features a rotating barrel equipped with two to three interchangeable grading barrels. These barrels have parallel bars that help in sorting the seeds as they move through. As seeds pass through the grading barrel, they fall into handling bins categorised by size. The choice of barrel size and the level of automation depend largely on the operational scale and the volume of seeds being processed.
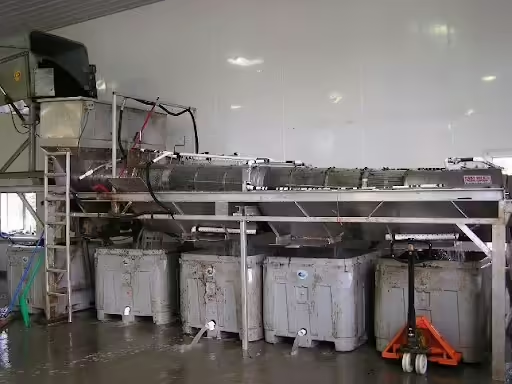
Large operation grading machine.
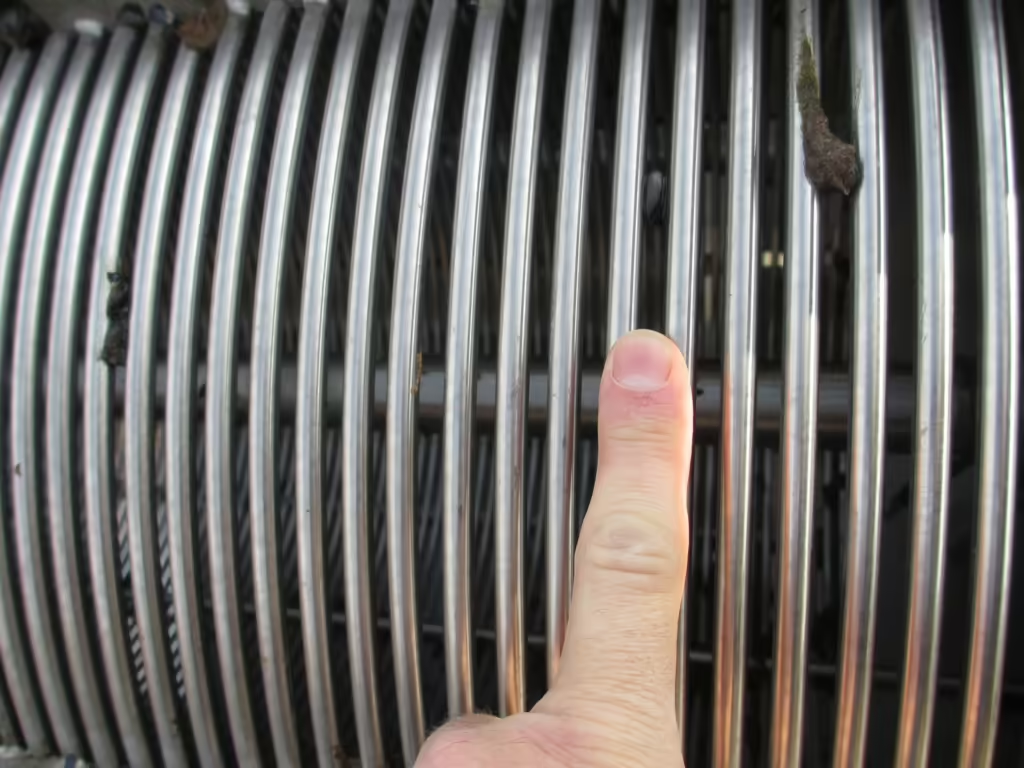
Grading Barrel for the smallest seed.
Step 3: Socking the Graded Seeds
After grading, each seed size is carefully matched with an appropriately sized mussel sock tube. This step is critical as it ensures uniform seed density within the tubes, promoting consistent growth rates. As seeds grow, larger tubes are used to maintain a uniform number of mussels per unit length, which is vital for both growth management and eventual harvesting.
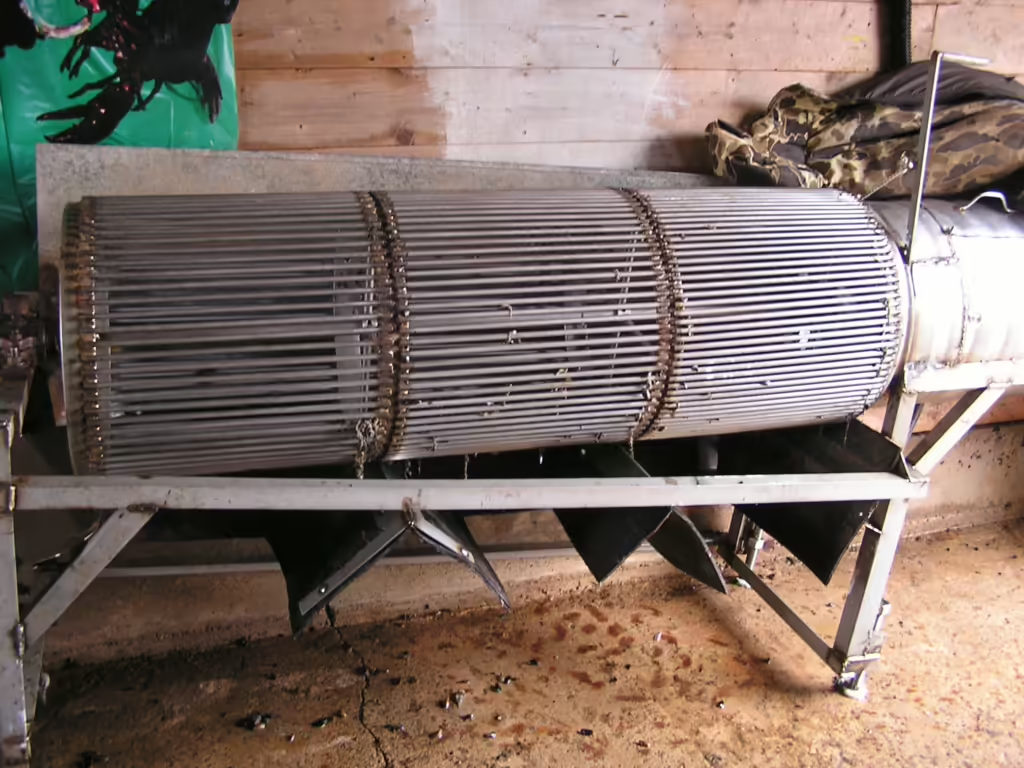
Small Operation Grading Machine.
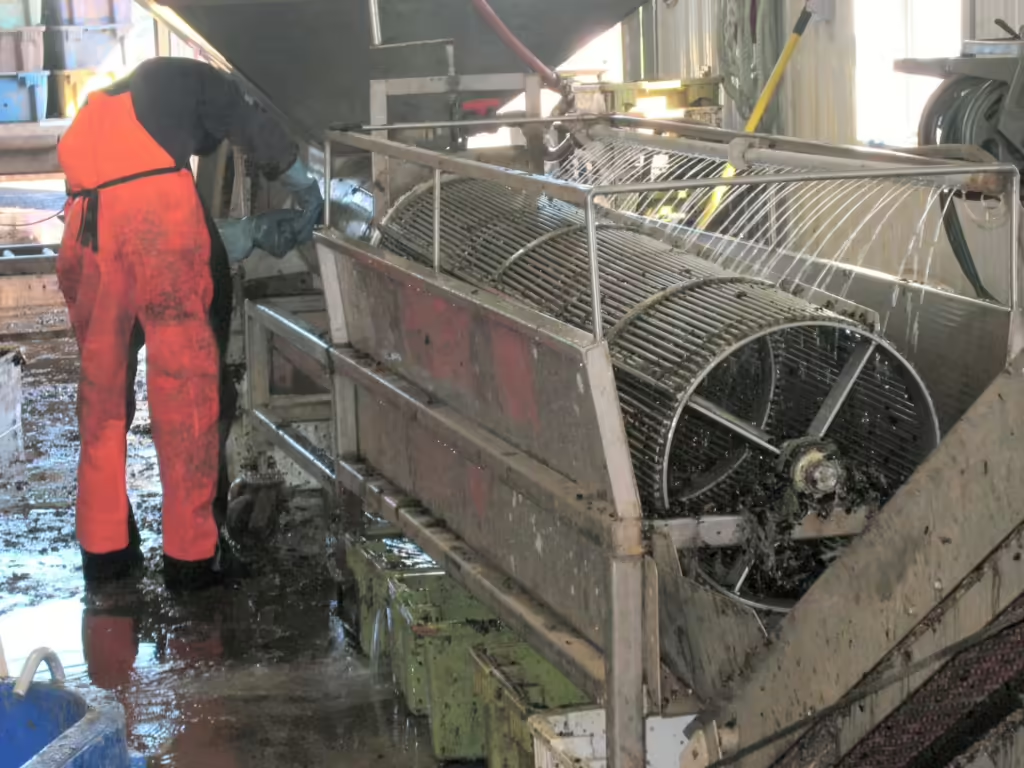
Small Operation Grading Machine.
The Benefits of Effective Seed Grading
Grouping seeds by size not only streamlines the farming process but also enhances the growth efficiency. Larger, faster-growing seeds are placed together, as are the smaller, slower-growing ones. This grouping ensures that mussels develop similar physical characteristics, leading to uniformity at harvest. Such uniformity is advantageous during the grading of the final product and can significantly increase the market value of the harvest.
Moreover, this method staggeringly extends the harvest window. Tubes containing larger seeds are harvested earlier than those with smaller seeds, thus optimising the harvest timeline and improving overall efficiency.
Understanding Mussel Socking Tubes in Aquaculture
Mussel farming is a specialised aquaculture practice that benefits significantly from the use of mussel socking tubes. These tubes are crucial for managing the density and distribution of mussels as they grow. Selecting the appropriate diameter of the mussel socking tube is essential, as it determines the “socking density,” which is the number of mussels that can be comfortably housed within the tube. This choice is also influenced by the size of the seed mussels being used.
As mussels mature, the diameter of the socking tube plays another vital role. A larger tube diameter means a larger mesh opening, which facilitates an important phase in the life cycle of the mussels: migration. During this phase, mussels move from the interior to the exterior of the tube. This migration is critical as it is outside the tube where the mussels continue to grow until they are ready for harvest.
The exterior of the mussel socking tube serves as more than just a boundary; it becomes a vital growth surface. The mesh of the tube acts as a substrate for the mussels’ byssal threads—strong, silky fibers that mussels produce to anchor themselves. The grid design of the mesh allows these threads to pass through and attach securely, providing a stable living environment for the mussels. This secure attachment is key to reducing the loss of mussels, commonly referred to as “fall off,” which can impact the yield and efficiency of mussel farming operations.
Understanding these elements of mussel socking tubes can help optimize mussel farming techniques, leading to more sustainable and productive aquaculture practices.
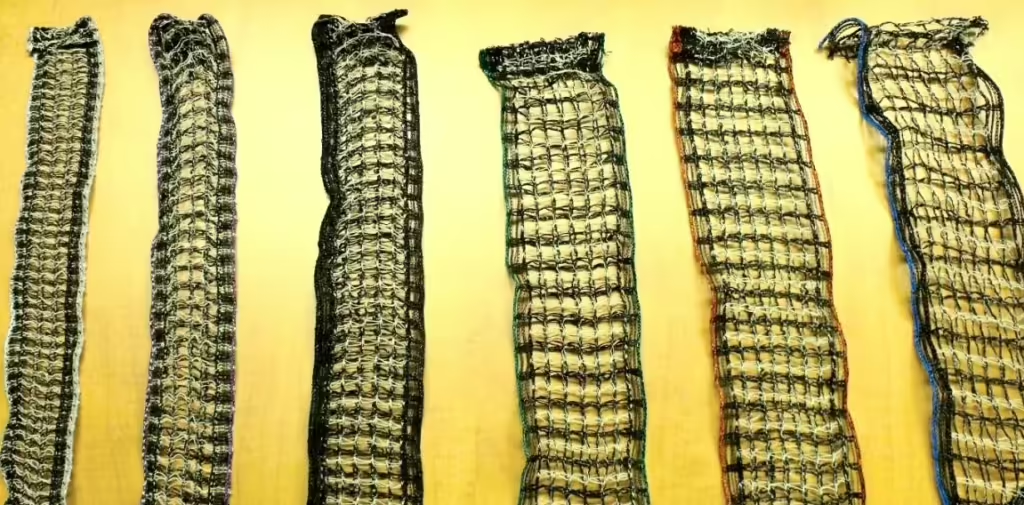
Tidal Marine Mussel Socking Tubes.
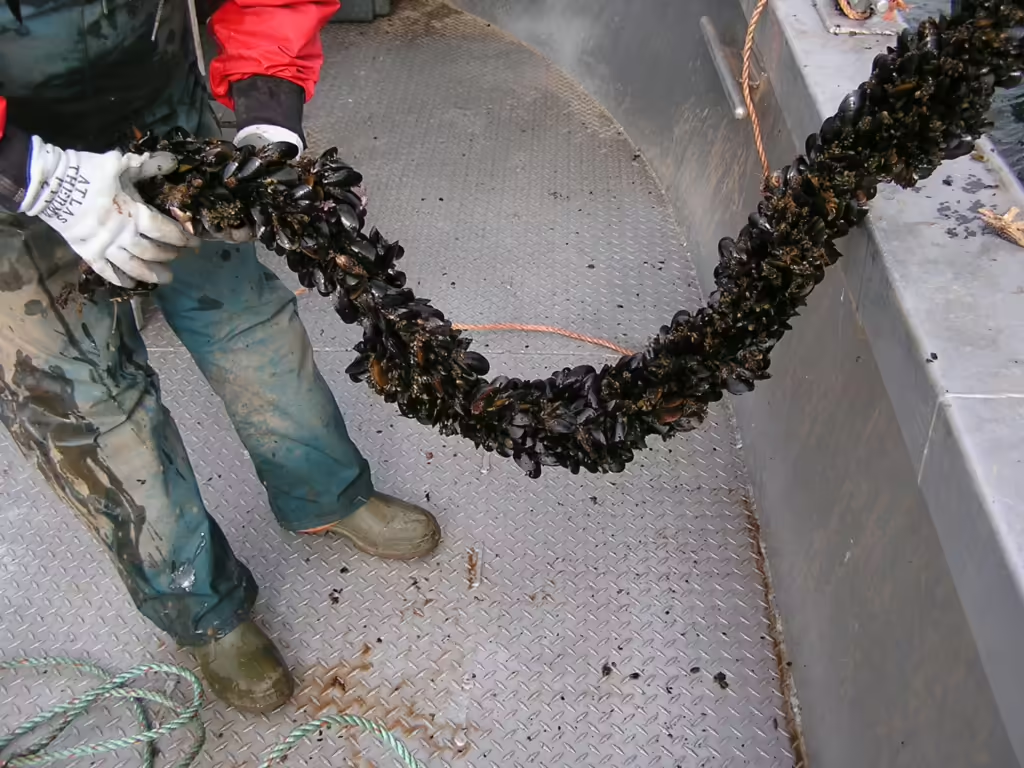
Mussels attached to the Tidal Marine Mussel Socking Tubes.
Advanced Features of Mussel Sock Tubes for Efficient Farming
Mussel sock tubes are designed to enhance the productivity and sustainability of mussel farming. These tubes are constructed from a square mesh made of interwoven strands, featuring reinforced bands along the sides. This design significantly increases the strength of the socks and prevents longitudinal elongation, or stretching, ensuring the tubes maintain their shape and effectiveness over time.
A standout feature of these mussel sock tubes is the use of water-soluble, biodegradable strands integrated between the square mesh openings. This innovative approach offers substantial benefits over traditional mussel socking methods. During the initial phases of mussel farming—such as socking, handling, and transferring, as well as when securing the socks to longlines or rafts—these biodegradable strands play a crucial role. They help contain the mussel seed, markedly reducing the loss of seed caused by shake-out.
These biodegradable strands are designed to last approximately three to six weeks. After this period, they naturally break down, which allows the mussels to migrate out of the sock effortlessly. This timed degradation is carefully calibrated to coincide with the growth cycle of the mussels, facilitating a smooth transition from containment within the sock to free growth outside it, thereby optimising the growth environment and improving overall yield in mussel farming.
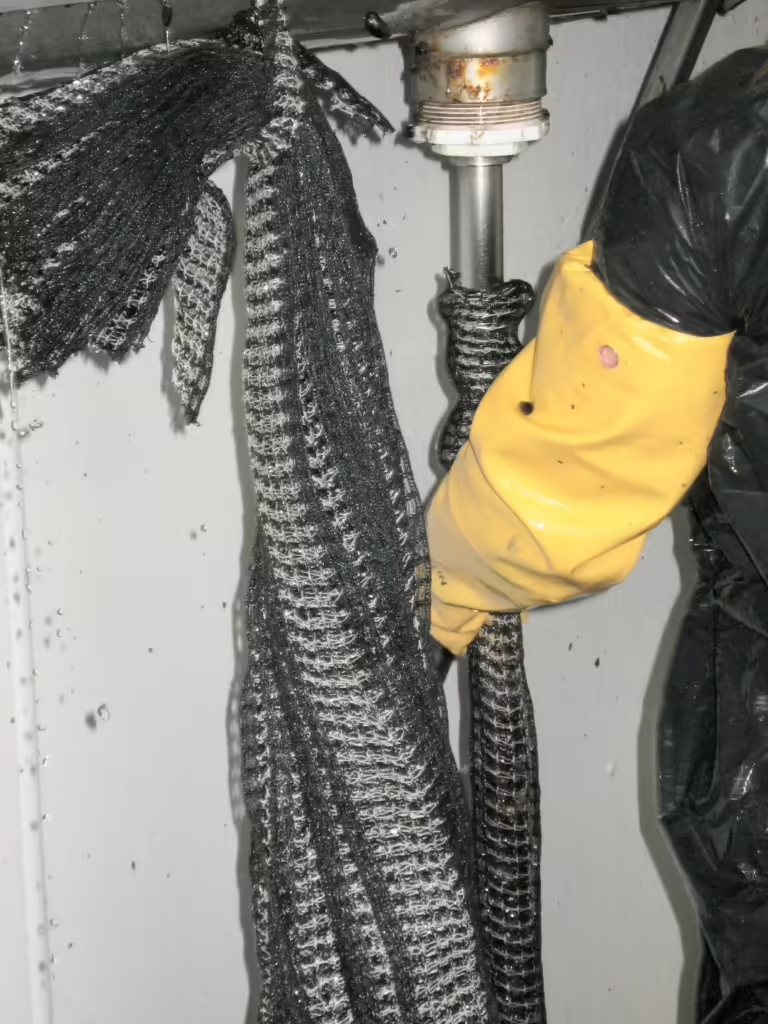
Mussel Socking Tubes – Ready-For-Use (1,000 socks per Bale).
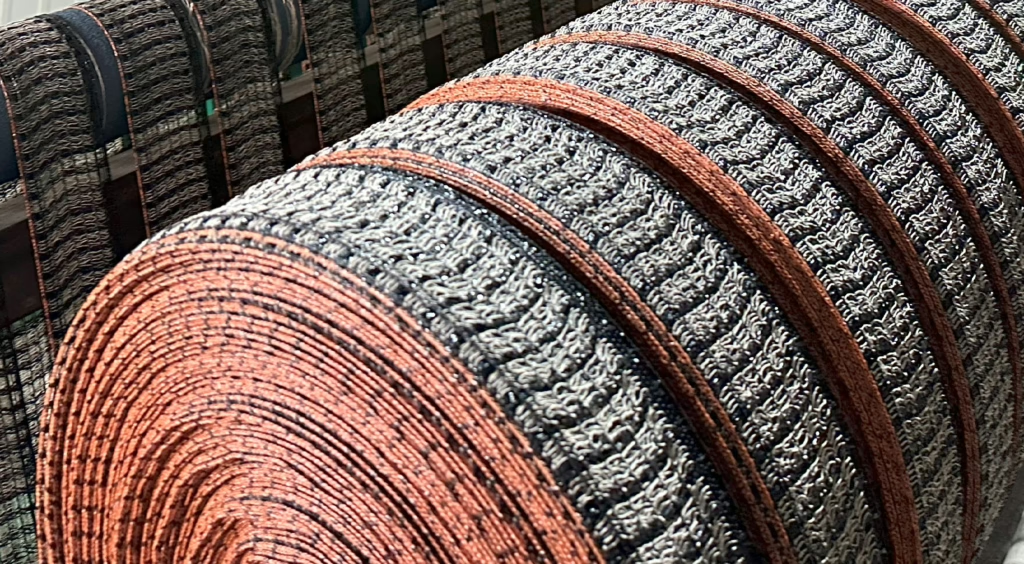
Mussel Socking Tubes in Rolls (5 Bands at 200m per Roll).
Mussel socking tubes are an essential component in modern mussel farming, providing an efficient and organised method for growing and harvesting mussels. These tubes are specifically designed to meet the varied needs of tidal marine industries.
Features of Mussel Sock Tubes
Mussel sock tubes come in various sizes, each easily identifiable by their unique colour coding. This feature simplifies the process of selecting the appropriate tube size for different farming scales and mussel types, enhancing operational efficiency.
Product Variants and Customisation
Our mussel sock tubes are available in two main formats:
- Standard Length: Sold in continuous lengths of 200 meters, these tubes are ideal for large-scale operations that require customisation on-site.
- Ready-to-Use: These are pre-cut and pre-sewn at one end according to the customer’s specifications. This format is particularly convenient, allowing immediate use upon delivery.
Packaging and Distribution
In the ready-to-use format, the sock tubes are meticulously organised into master bales of either 500 or 1,000 units. Each master bale contains sub-bundles of 50 socks, facilitating easy inventory management, housekeeping, and production flow in your mussel farming operation.
Handling and Operation
The process of filling the mussel socks is streamlined and adaptable to the size of the mussel farming operation. The graded mussel seed is efficiently transferred from the grading machine to the sock filling equipment. For smaller operations, transfer is managed with small totes, while larger setups may use big boxes moved by forklifts or integrated conveyor systems, ensuring that scalability and volume needs are met without compromising on efficiency.
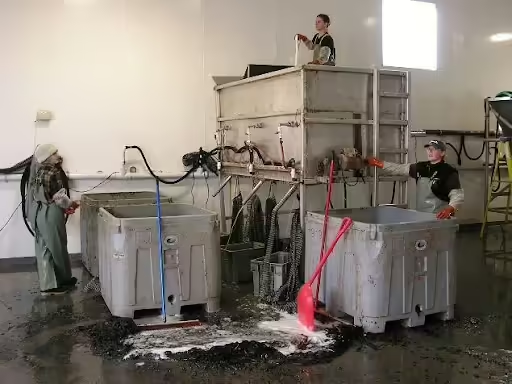
Mussel sock tube filling stations.
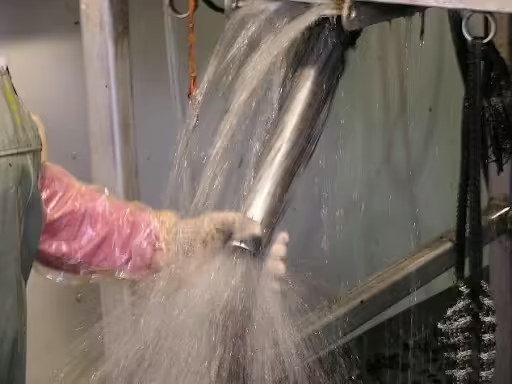
Gravity and water flow fill the socking tube with seed.
Mussel socking tube filling equipment is designed to accommodate the diverse needs of mussel farming operations, ranging from straightforward manual setups to more advanced systems featuring multiple filling stations and automated handling mechanisms.
Key Features of Filling Equipment
The essential components of both simple and complex filling systems include:
- Hopper: Equipped with a water supply, the hopper serves as the initial loading point for the mussel seed.
- Filling Pipe: Tubes are manually loaded onto a filling pipe that features a sliding gate valve, strategically placed between the hopper and the pipe to control the flow of seeds and water.
Operation Process
During operation, the sock tube is secured onto the filling pipe. Once in place, the sliding gate valve is opened, allowing the water and mussel seed to flow by gravity into the socking tube. The weight of the contents naturally pulls the sock down from the pipe as it fills. When the sock is full, the gate is closed to halt the process.
Our proprietary socking tubes are designed with a fixed diameter to prevent ballooning as the seed fills the tube. This feature ensures that each sock maintains consistent density, providing uniform quality across all harvested mussels. Moreover, the straightforward design of our system requires minimal training, allowing new employees to quickly master the filling process and contribute effectively to production.
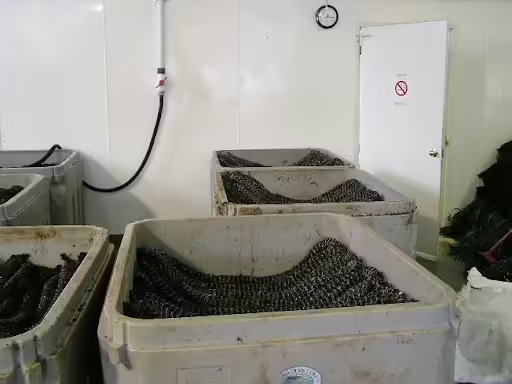
Socks filled with seed.

Transfer of socks to a workboat.
Storing and Transferring Filled Socks
Once the mussel socks are filled, they are carefully placed into boxes designed for both protection and ease of transport. These boxes are then ready for the next phase of the mussel farming process.
Deployment to Growing Sites
The filled and boxed socks are transported to the growing sites, where they are methodically hung on longlines. This setup is crucial for the proper development and growth of the mussels in their natural marine environment.
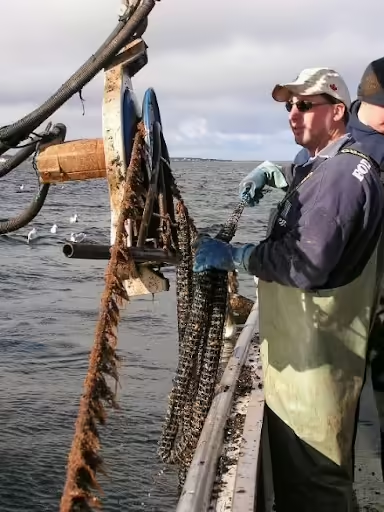
Socking tubes are tied to the longline.
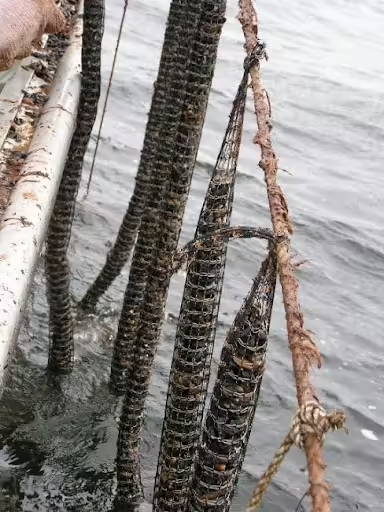
Socks at 60 cm spacing on the longline.
Raising and Positioning the Longlines
At the farm site, the process of setting up the mussels for growth involves intricate manoeuvres with the submerged longlines. As the workboat moves along the line, these longlines are carefully lifted over a device known as the star wheel, facilitating precise handling and positioning.
Securing the Socks
Once elevated, the socks, each featuring a “tail” end, are securely tied to the longline. This method ensures that the socks are well-positioned and stable, crucial for the growth phase of the mussels.
Determining Sock Spacing
The spacing between each sock is adjusted according to the specific growing conditions of the site. Typically, the socks are positioned 60 centimeters apart, allowing ample space for optimal growth and ease of maintenance.
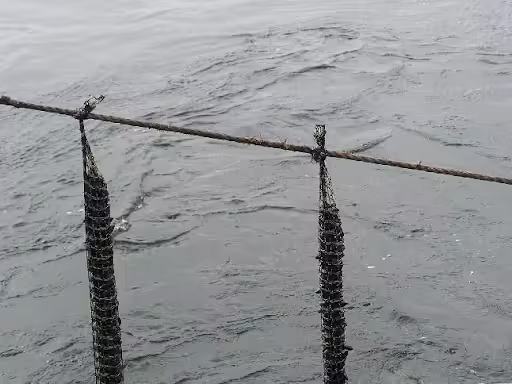
Socks and longline descending from Star Wheel.
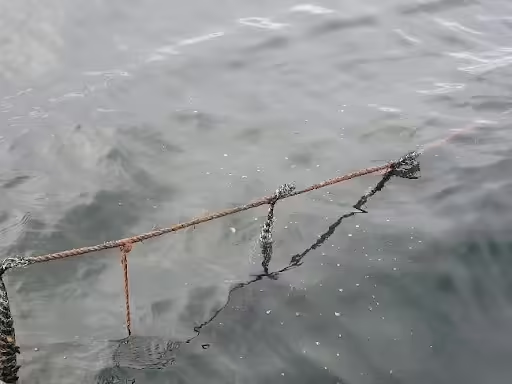
Sinking of the longline as the process continues.
The deployment process is designed to be continuous. As the workboat progresses, the longline gradually sinks back into the water, returning to its designated depth for safe and effective mussel growth. This ensures that the mussels are well-positioned in their natural habitat to thrive.